At Glenroy, Inc., a flexible packaging manufacturer in suburban Milwaukee, they understand the benefit of going green. Coupled with major process initiatives such as converting natural gas drying of their printed films to heated compressed air, Glenroy has partnered with Heritage-Crystal Clean (HCC) to make these initiatives easier to implement.
Of course, in the machine shop, Glenroy has one of Crystal Clean’s tried and true 40-gallon parts washers with solvent that is changed out on an eight-week service interval and recycled as a part of Crystal Clean’s reuse program.
Some of the maintenance and engineering crew that take care of the converting machines on the shop floor are pleased with the quality of the solvent as well as the mechanics of the parts washer. “Our old parts washer always had problems with the pump and the solvent never seemed to stay clean” said Ned Lange, who manages a crew of 13 mechanical and electrical technicians. “Since we got rid of the old parts washer and had Crystal Clean’s machine and solvent service in place, I’ve had nothing but positive comments from my guys – whenever we have to change out a gear box or just clean up some old dirty parts, the solvent always does the job and the pump works like it did on the first day we had it – and their service is great!”
Another way Crystal Clean has helped Glenroy better manage its environmental issues has to do with the two Aqua-Filtration-Service (AFS) units installed to remove tramp oil from the compressor blowdown. Glenroy has multiple banks of compressors to provide compressed air to the entire facility. Before the AFS units were in place, they had various problems with oil and water in the air lines and the basic oil-water separator they had in place never really did the trick. Since the units have been installed, the regular 16-week service interval had to be adjusted for the seasons.
Crystal Clean’s exceptional customer service from the Milwaukee branch worked with Ned and Jim Hillstrom, Glenroy’s Manager of Regulatory Compliance, to adjust for the changes in humidity. Now, wintertime has the AFS units serviced on the original
16-week interval, but in summer with the increased humidity, the AFS units are changed out every eight weeks. Bill Kopecky, manager of the flexographic printing department that utilizes the heated compressed air to dry the printed films, states “since we had the Crystal Clean AFS units installed, the air going to the press dryers is clean and dry like it should be.”
And that’s not the only place where Glenroy and Crystal Clean partner. Every year or so, Bob Gonzales, branch sales manager at HCC’s Milwaukee branch helps Mr. Hillstrom put together a lab pack inventory to remove older and spent chemicals that accumulate at Glenroy. And of course, when Jim has drums of waste to be removed, Crystal Clean is a phone call away, and Jim loves their customer service. “The route driver is always friendly, on time and well prepared to remove whatever we have, whether it be waste coolant or process sludge.”
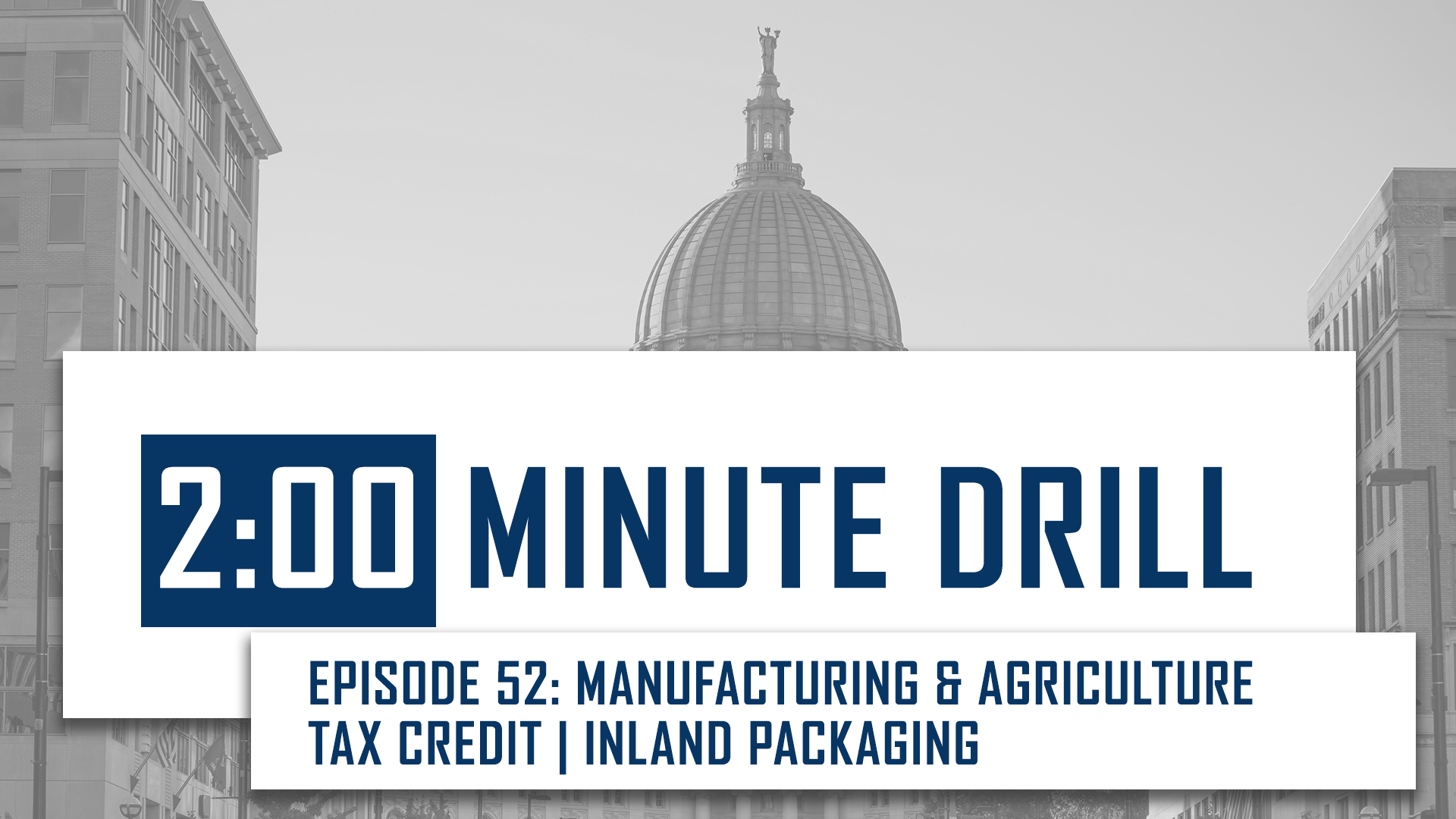
Episode 52: Wisconsin’s Manufacturing & Agriculture Tax Credit
https://www.youtube.com/watch?v=-enjM36-GAk WMC, in partnership with Inland Packaging in La Crosse, released a new video highlighting how Wisconsin manufacturers have contributed to the state’s economy due